The flip front that came with my car tricked me in to a false sense of security, I thought it would save a ton of work and allow an easy way to access the engine when needed . Trouble is my car is a Prefect and the front end is for an Anglia, it's also been very badly hacked about so it is no longer rigid and I suspect it wasn't of the finest quality in the first place. To add to my woes the metalwork on my car has been extensively messed with and nothing really lines up any more.
I have already mentioned many times that body work really isn't my thing, I am better at knitting fog than I am at tin bashing so this is all a bit of a challenge. I have concluded that the first thing I need to do is get some rigidity back in to Freddy the floppy flip front and start to get some reference points that I can work from. To that end I found some old bits of wood - like all the best hot rod builders do - and set about making a frame to hold the rear most parts of the fibreglass moulding. First I used the original Ford bulkhead to give me the correct curvature for a piece of wood to go across the top of the bonnet, a simple job with a jigsaw, I can drill holes in the bonnet for screws to hold it all together, they should be really easy to fill without leaving a trace when I am done. With that fixed securely in place the bonnet is already much stiffer but the two arches still flop about more than that time floppy the flop fish got stuck in half a pair of flip flops. That's easily rectified now though as I can do a similar trick to the top bit and secure vertical strengthening pieces to the over length top piece to hold the two arches in the correct place. I have used a couple of jacks to put the lower edges of the arches in the right place, I used the wheels as a guide to make sure everything was hunkey dorey - which as you all know is another kind of fish. I know that probably doesn't make sense, please see the attached photos and ignore anything I said about fish.
So with it in the right shape I can now take the whole thing off, turn it upside down and glass in 5 mm round mild steel strengthening pieces. I chose 5mm as it's thin enough to bend with simple hand tools but stiff enough to give the rigidity I need. It's quite cheap and available in long lengths, fibreglass reinforced repair paste will be used to fix the formed rods in place, the whole thing should be very strong without adding too much weight.
The idea is that when it is all dry I can start replacing the missing material knowing that everything is in the right place. It's all very cunning but I have no idea for sure if I am doing the right thing or not - time will tell.
I reckon once that is done the next logical thing to do is to make the running boards - IVA rules have to be adhered to here as I need to put quite a large radius on the edge of them. I am thinking of using a trick I saw Bad Chad do once and use a length of exhaust pipe or similar to give me a nice uniform curve with enough radius to make even the most zealous of profile gauge wielding inspectors squeal with delight. It will make the running boards really strong too, which is proper bonus. The top of the board will be 2mm or so thick steel sheet with strengtheners and several brackets to stop it from flexing, ribbed rubber will be glued on top of that to make it nice and grippy. I think the car will look much nicer with running boards, I sort of saw them in my mind's eye when I first stupidly agreed to build this thing.
The metalwork needs sorting where the flip front meets the original Ford metalwork, I have 2 ideas as to how I want to do it, I shall reveal my cunning plan when I have decided which way to go. I have to work out a solution that works and that I am confident to do and do well, no point doing something complicated and making a balls up of it.
Just making the arches line up properly makes the front look so much better that it has given me some encouragement to get on with it and make it right, it's very easy to lose confidence on a project like this especially when you are working by yourself and doing a lot of things for the first time. my aerial arrived today - I have to confess to having completely forgotten the obvious fact that if I want a radio I need an aerial - dooooh. My current head unit is FM only but I am fitting an amplified DAB compliant aerial so I am free to upgrade in the future without having to remove half the interior if I decide to upgrade.
I just remembered that I ran out of cable ties a few months back when i was fitting the replacement alternator - I must fit some to retain the cables, it would be a serious bummer to get a fail for such a minor thing.
Another job I need to do is take my carbs to bits again, now it's cold I have discovered that the chokes are not working correctly and it's a complete mare to start when it gets down to anything below about 5 or ten degrees. I think the bits that rotate in the SU's to uncover the enrichment ports have o rings fitted that are leaking air and so extra fuel is not being sucked in like it should be. That's only a guess at the moment but I know that once the engine has been running for about 20 seconds it settles down and behaves itself, it's proper naughty before that. It's not a big deal although getting the seals without buying a complete kit may be a challenge and they are really expensive. Oh well nobody said it would be easy.
-------------
Bit of an update, I had to walk away from it for a while, I was really struggling to work the flip front fitment out and was getting quite emotional about things - it's at times like this so many projects get abandoned. Fortunately there are groups on facebook etc where there are people that have gone through this before and are able to offer useful words of advice. It was following such an interaction that it occurred to me that the reason nothing fitted is that the metalwork I was trying to match up to was not original Ford metal but something somebody had added for some inexplicable reason, maybe they did it out of spite - who knows?
Anyway with that piece of knowledge I went back to the workshop, with angle grinder in hand and a whole new level of determination. Sure enough when I cut off the bit that had me stumped it became obvious somebody had added bits on, quite why they had done it like they had was not obvious, the rotted out original Ford steel was behind it, full of holes and with 4 mm of filler over it. Now that is all cut out the solution is obvious, I just need to crack on and get it done, tomorrow I shall go to my favourite steel supplier and exchange money for a sheet of 1mm thick steel. I can make cardboard templates and then steel panels to fill in the bits that need filling in. I will also get some ally sheet to help me remake the bits of the fibre glass front that somebody cut away. It's a fair chunk of work but at least I can see the solution now so I feel a lot better about things.
Latest video is on youtube - linkypoo here -
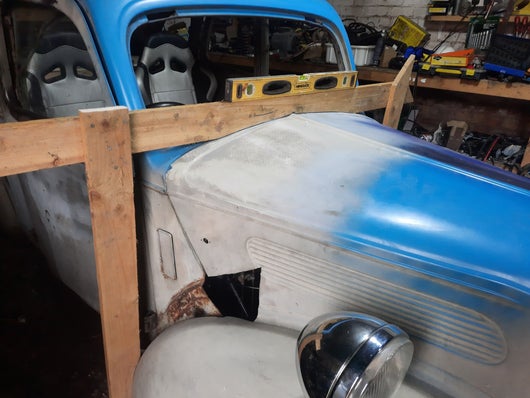
A simple wooden frame helped to hold things rigid so I could measure up, I later added some diagonals to hold it even better, the level allowed me to check I wasn't twisting anything.
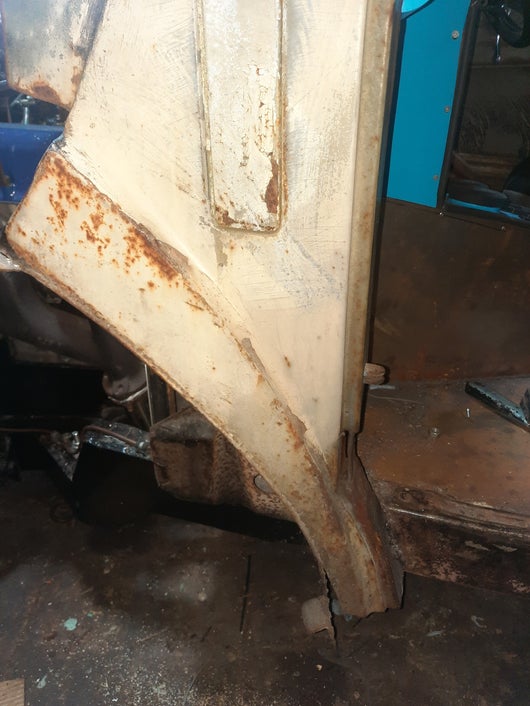
I thought these bits were original but it turned out they had been added at some time and were making my life difficult, the angle grinder was deployed.
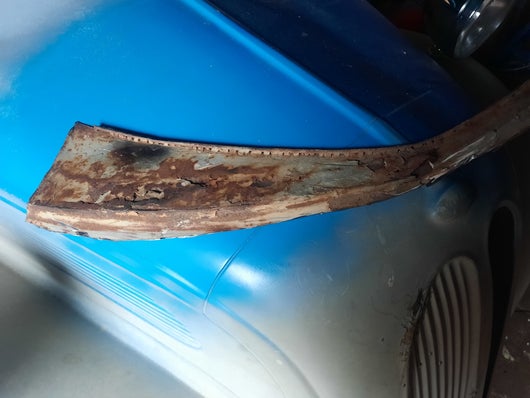
One of the added bits after I de-added it. I taught it a lesson in humility that it will never forget. Once removed I could see the rotten old Ford metal, a 4mm layer of filler and then the new steel on top of that - not very nice, I'm glad I have shot of that.
Add comment
Comments
Brilliant stuff Mr P !