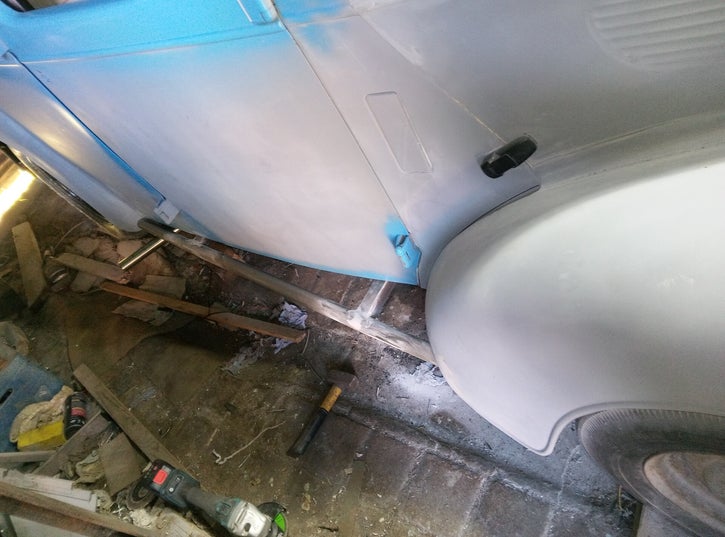
Driver's side before the steel sheet gets welded down.
Having procured the stainless steel tube at last week's visit to Normous Newark autojumble, I had no excuses left, it was time to get on with the running boards, or side skirts, if you prefer. I had no way of making an appropriate curve in a piece of metal that big so using the tube worked around that problem. I cut two recesses in each piece which accepted square steel tube, which I could then cut to length and weld to the existing chassis rails. I figured two each side would be plenty strong enough, This proved to be the case when I tested them by jumping up and down on each one. I reckon that's how Aston Martin do it although they probably use a proper fat bloke rather than a cut price old bloke that's only fat around the middle.
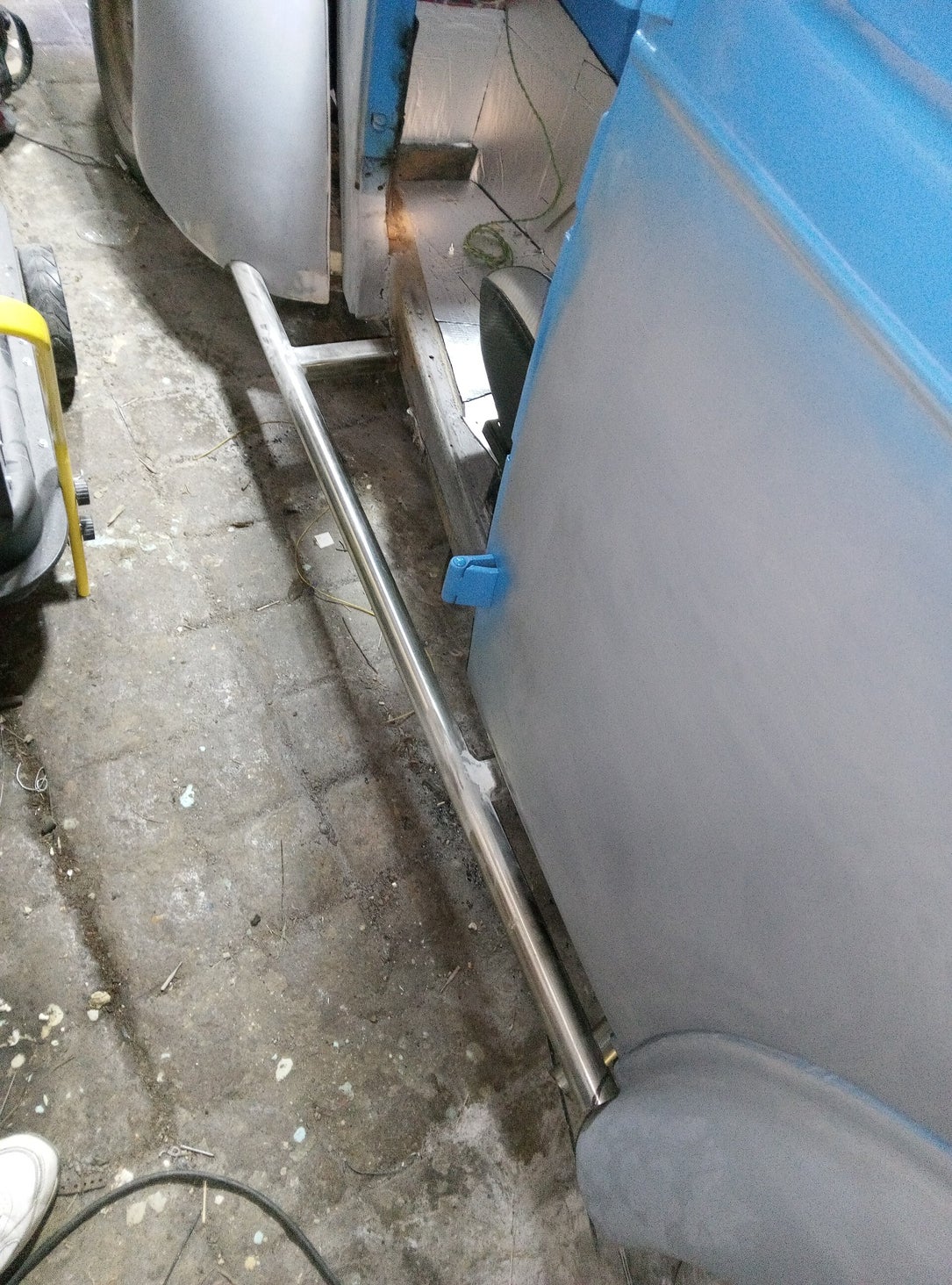
Passenger side looking from the rear towards the front. The bonnet will close against curved strips, which I have not made yet. You can just make out the end of the exhaust pipe emerging from just in front of the rear wheel arch.
I had to buy some special welding rods - 309L ones which are specially formulated for welding mild steel to stainless. I should have got much thinner ones as the 2.5m ones I got kept blowing holes through, which required some very careful low amp welding to fill back in. It took far longer than it should have done to get a job I was happy with. The jump test showed the work to be more than adequate so all's well that ends well. The job will be finished off with some 2mm steel plate over the top of it, that will then get some ribbed rubber glued to it but that won't happen until after the paint has been applied.
I used some tubing that was the same size as the tailpipes, so that was the next job. I did have a pipe bender but I sold that so had to cut vees out, bend the pipe and weld it back up, I learnt from the side step job and used my mig welder, much better. I used a torch to make sure there were no pin holes, I found one on one side but apart from that they are fine. Making two the same was a bit of a challenge with the tools available and I had to try twice on the second one but it's all good. I can't finish the job as I need some Gun Gum sealant, a couple of clamps and some rounded over end tips to meet the IVA requirements. They will come out just in front of the rear wheels, they will look cool and negate the need for complicated pipework and bends going over the rear axle.
I have no idea if the car will pass the noise test, my plan is to drill holes in the tubes so I can fit what they call db killers - basically short baffles that go in the end of the exhaust to kill the noise. They are really bad for killing power too but will do the job to reduce the sound level if needed. The Jaguar silencers do a very good job and I don't think it will be too loud, they measure the sound output at 3/4 max revs with a microphone at 200mm height and at 45 degrees to the exhaust outlet, the max level allowed is 99dbA, which is actually a fair bit louder than for modern cars at just 72dbA. For comparison human voices are round about 60 dbA, unless you are Noddy Holder out of Slade, in which case it's about 12 times that. I'll have a look to see if there is an app for my phone that will give me a rough idea.
Add comment
Comments